Working pressure: the actual pressure of the input motor oil, which depends on the load of the motor. The difference between the inlet pressure and the outlet pressure of the motor is called the differential pressure of the motor. Rated pressure: the pressure that enables the motor to work continuously and normally according to the test standard.
2. Displacement and flow(hydraulic motor)
Displacement: the volume of liquid input required for each revolution of the hydraulic motor without considering leakage. VM (m3 / RAD) flow: the flow without leakage is called theoretical flow qmt, and the leakage flow is considered as actual flow QM.
3. Volumetric efficiency and speed(hydraulic motor)
Volumetric efficiency η MV: ratio of actual input flow to theoretical input flow.
4. Torque and mechanical efficiency(hydraulic motor)
Without considering the loss of the motor, its output power is equal to the input power. Actual torque T: torque loss due to actual mechanical loss of motor Δ T. Make it smaller than the theoretical torque TT, that is, the mechanical efficiency of the motor η Mm: equal to the ratio of the actual output torque of the motor to the theoretical output torque
5. Power and overall efficiency(hydraulic motor)
The actual input power of the motor is PQM and the actual output power is t ω。 Total motor efficiency η M: The ratio of actual output power to actual input power. There are two circuits of hydraulic motor: hydraulic motor series circuit and hydraulic motor braking circuit, and these two circuits can be classified at the next level. One of the series circuits of hydraulic motor: connect three hydraulic motors in series with each other, and use a directional valve to control their start, stop and steering. The flow of the three motors is basically the same. When their displacement is the same, the speed of each motor is basically the same. It is required that the oil supply pressure of the hydraulic pump is high and the flow of the pump can be small. It is generally used in light load and high-speed occasions. Hydraulic motor series circuit 2: each reversing valve in this circuit controls a motor, each motor can act alone or at the same time, and the steering of each motor is also arbitrary. The oil supply pressure of the hydraulic pump is the sum of the working pressure difference of each motor, which is suitable for high-speed and small torque occasions. One of the parallel circuits of the hydraulic motor: the two hydraulic motors are controlled by their respective directional valves and speed regulating valves, which can operate simultaneously and independently, regulate the speed respectively, and basically keep the speed unchanged. However, with throttling speed regulation, the power loss is large. The two motors have their own working pressure difference, and their speed depends on their respective flow. Parallel circuit 2 of hydraulic motor: the shafts of the two hydraulic motors are rigidly connected together. When the directional valve 3 is in the left position, motor 2 can only idle with motor 1, and only motor 1 outputs torque. If the output torque of motor 1 cannot meet the load requirements, place valve 3 in the right position. At this time, although the torque increases, the speed should be reduced accordingly. Hydraulic motor series parallel circuit: when solenoid valve 1 is energized, hydraulic motors 2 and 3 are connected in series. When solenoid valve 1 is powered off, motors 2 and 3 are connected in parallel. When the two motors are connected in series through the same flow, the speed is higher than that when they are connected in parallel. When they are connected in parallel, the working pressure difference of the two motors is the same, but the speed is lower.
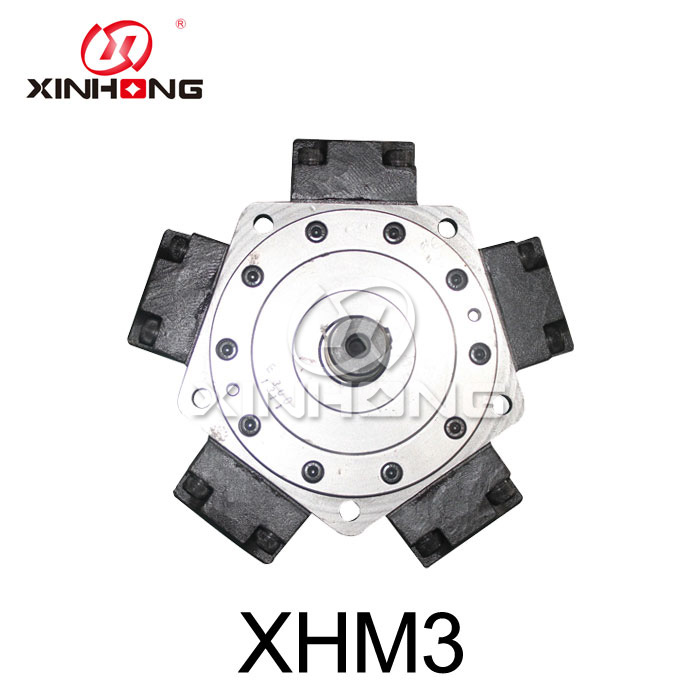